浮動円板を用いた可変絞り型静圧気体スラスト軸受(静的特性)
Aerostatic Thrust Bearing with a Self-Controlled Restrictor Employing a Floating Disk (Static Characteristics)
TOP
BACK
Aerostatic bearings have been successfully applied to ultraprecision machine tools and precision measuring equipment because of their attractive features such as low friction, cleanliness and high accuracy of motion. These devices often require higher stiffness rather than larger load capacity to improve their accuracy. In order to achieve higher stiffness in aerostatic bearings, it is effective to design the bearings so as to obtain the maximum stiffness in bearing clearance as small as possible. various types of bearings have been proposed based on this concept. However, it is naturally considered that there is a limitation in reducing bearing clearance and obtaining higher stiffness, when taking into account the manufacturing accuracy.
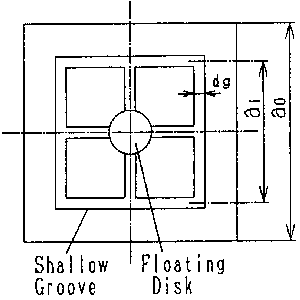
Fig.1-1(a) The proposed aerostatic thrust bearing with a self-controlled restrictor employing a floating disk
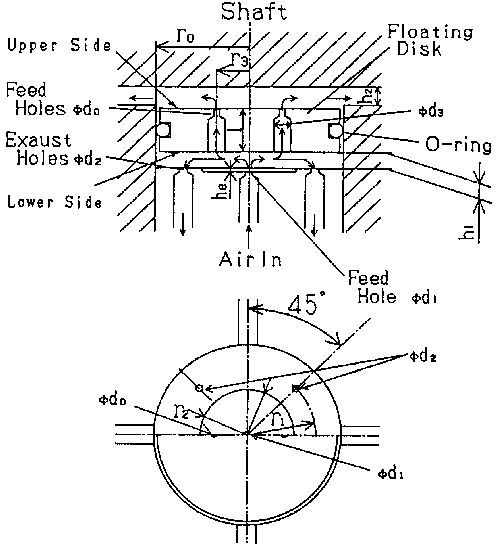
Fig.1-1(b) Details of the self-controlled restrictor
Another means to achieve higher stiffness is to use self-controlled restrictors. Until now, many types of aerostatics bearings with self-controlled restrictors have been proposed and most of them employed diaphragm restrictors. However, the following difficulties exit in using diaphragm restrictors.
(1) It is difficulties to select the optimum design parameters to obtain very high stiffness because of the severity of tolerances of design parameters.
(2) It is difficult to maintain high stiffness when supply pressure and applied load are varied widely.
(3) This type of bearing is prone to cause a pneumatic hammer.
The author proposes a new type of self-controlled restrictor employing a small floating disk to avoid the disadvantages of diaphragm restrictors. This self-controlled restrictor can have very stiffness in a wide range of applied loads independent of supply pressure.
In this paper, the static characteristics of the proposed bearing are investigated theoretically and experimentally. Furthermore, the optimum design method to obtain very high stiffness is discussed.
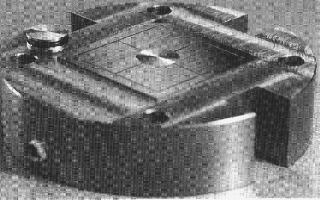
Photo 1
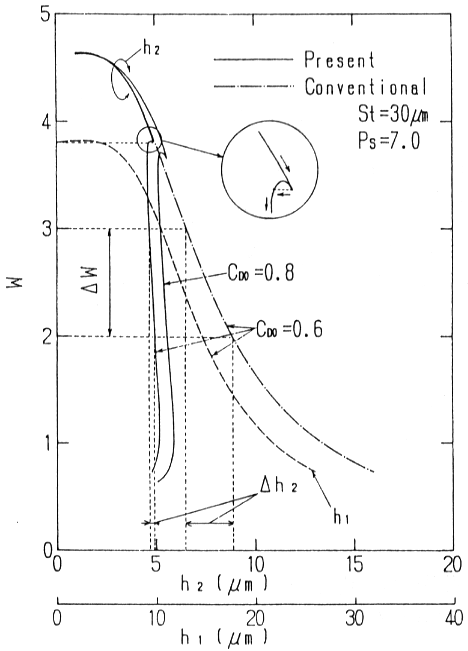
Fig.1-2 Static characteristics of the proposed bearing